Auger powder filling machines are extensively used in the packaging industry for filling and sealing dry powder products. These machines are also useful for liquid filling and stoppering applications. They ensure precise and consistent filling of products in containers like bottles, vials, and jars, making them ideal for pharmaceutical, chemical, and food industries. In this article, we will explore the essential features of auger powder filling machines and provide tips on selecting the best one for your business.
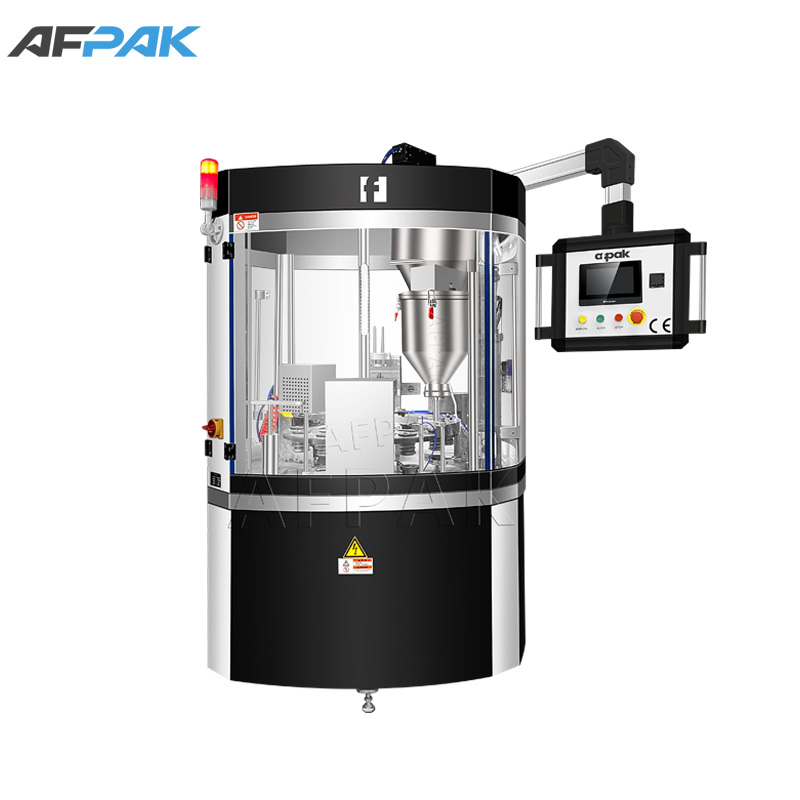
Types of Auger Powder Filling Machines:
There are two primary types of auger powder filling machines, which include:
1. Servo-Driven Auger Fillers: These machines use a servo motor to drive the auger, which dispenses the powder into containers. They are known for their high accuracy and consistency in filling products, making them ideal for applications requiring precise measurements.
2. Volumetric Auger Fillers: These machines measure the product volume using chambers or pistons and then dispense it through the auger. They are suitable for filling predetermined volumes of products, making them ideal for applications where consistency is essential.
Features of Auger Powder Filling Machines:
1. Hopper: The hopper is where the product is loaded for filling. It should be constructed with high-quality materials and be large enough to hold sufficient quantities of the product.
2. Auger: The auger is a screw-like mechanism that dispenses the product into containers. It should be designed to handle different types of products, such as powders, granules, and flakes.
3. Filling Nozzle: The filling nozzle dispenses the product into the container. It should be adjustable to accommodate various container sizes and shapes.
4. Control System: The control system manages the machine's speed, filling accuracy, and other parameters. It should be user-friendly and allow users to adjust settings easily.
5. Cleaning System: The machine should have a cleaning system that facilitates quick and efficient cleaning between product changes, preventing cross-contamination.
Tips for Choosing the Best Auger Powder Filling Machine:
1. Product Specification: Consider the type of product you intend to fill and its physical properties like consistency, viscosity, and particle size. This will help you determine the right type of auger powder filling machine for your application.
2. Production Capacity: Determine your production requirements, including the quantity of product to be filled, the speed needed, and the number of containers to be filled per minute. This will help you select the right machine size, speed, and number of filling heads.
3. Container Size and Shape: Consider the size, shape, and type of container you will be filling, including bottles, vials, jars, and pouches. The filling head should be adjustable and versatile enough to accommodate various containers.
4. Accuracy and Consistency: Choose a machine that provides accurate and consistent filling, reducing the amount of product giveaway and ensuring high-quality products.
5. Quality and Durability: Look for a machine made of high-quality materials that are durable and long-lasting. This will ensure that the machine is reliable and requires minimal maintenance.
In conclusion, auger powder filling machines are invaluable for businesses that need to fill dry powders and liquids accurately and consistently. By considering the critical features and tips when selecting a machine, you can ensure that you choose the right one for your needs. At (need to remove the brand name), we provide high-quality auger powder filling machines for various applications. Contact us today to learn more!
Keywords: Auger Powder Filling Machine, Servo-Driven Auger Fillers, Volumetric Auger Fillers, Product Specification, Production Capacity, Container Size and Shape, Accuracy and Consistency, Quality and Durability.